TPS Entry in the Cannabis Market, Q&A with Steve Scafaria
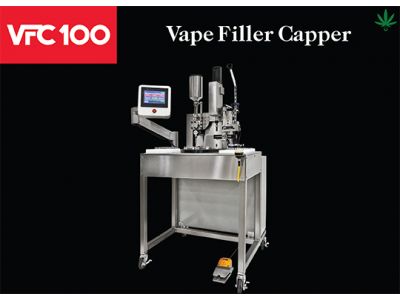
The cannabis industry’s legacy operators played a major role in the market’s transition from underground to legal, and they continue to influence how things are done as legal cannabis expands even further across the nation.
However, those that entered the industry from adjacent professions have also contributed significantly to today’s legal market – especially in regards to innovation and expansion.
Technical Packaging Systems has almost five decades of experience in the food and pharmaceutical realms, and they’ve brought that highly-regulated and safety-forward expertise to the cannabis industry in order to increase productivity, establish customer loyalty, and set impeccable standards for cannabis packaging.
We sat down with TPS’s president Steve Scafaria to discuss their entry into the cannabis market.
Leafwire: How was TPS initially founded?
Steve Scafaria: The company started back in the mid-to-late 1970s. It was originally a packaging supply equipment and distribution company, and it eventually morphed into more automation: specifically upstream from the process to end of line.
We recognized a need to offer more to our customers in terms of turnkey solutions, like packaging automation as well as product handling…a complete integrated solution for our partners.
LW: So, why the decision to service the cannabis industry?
SS: Let’s fast-forward to 2018, when Michigan’s adult-use cannabis market became legal. We picked up a couple of lines that would allow us to participate in the cannabis industry: a cone-filling line, and a cannabis grinder line. We had a couple of customers approach us with manual systems for other products that were very labor intensive and just didn’t work well.
That began our initial development of our machine, the VFC 100, vape filler capper. It took 2 to 3 years to develop. It was a difficult project because cannabis was a controlled substance, and we couldn’t have the oil in our facility.
LW: What sets you apart from competitors today?
SS: Our customer base is still over 50 percent food processing and pharmaceutical. We work within the confines of food safety, and all the equipment we sell has to be food safe and built with sanitary design in mind. Because of that, every machine we develop takes in all of those basic principles – and that’s very important for the cannabis industry, because it’s a human consumption product.
We saw what was out there for processors, and it didn’t make sense to us from what we understand about food safe automation – and for products processed for human consumption.
We started by building the VFC 100 – a machine that fills and caps cartridges inline, on the same platform or frame. Most other available technologies require two machines and a secondary process, like separate machines for filling and capping.
It made sense for us to have it all done in one process – especially for a product that needs to be closed or capped immediately. This eliminates cart leakage, possible contamination, and prevents consumer returns due to poor quality.
LW: What other innovations have you brought to the cannabis industry with your designs?
SS: Our machine is all electric. Most other technologies require an air compressor to operate and depending on the fillers air volume requirement, a compressor can cost anywhere from $15,000-$25,000. Our machine was built with the idea to keep developing, and as we learned more about the needs of our end user, we adjusted accordingly.
For example: the processor must have a filler that moves this often-viscous oil at a low temperature. If you overheat it, the product is ruined, or at the very least, terpenes are diminished. Our machine operates at a very low temperature to prevent that issue.
Also, from a capping standpoint, our system accommodates press-fit and screw-on caps. Rather than having to purchase yet another machine, ours will work with any type of mouthpiece.
We also have a (CIP) clean-in-place system. In between strains, it’s required that you clean your system out completely, because strains cannot be commingled. Our system’s cleaning cycle is entirely self-contained, so within approximately 15 minutes, you’re good to start the next production run.
LW: What have you found that is unique or challenging about working in cannabis?
SS: Our technology is unique, and no one really knows who we are yet in this industry – especially MSOs who haven’t had an opportunity to see our technology. We want to show more people the VFC 100 and keep building upon that base.
LW: What’s your favorite thing about working in cannabis?
SS: I’ve found it very enjoyable. It’s a new vertical to participate in, and it’s changing all the time.
LW: What’s on the near horizon for TPS?
SS: Right now, we’re working on further automation. Our system currently requires an operator, but our next development will aim to essentially run without one.